Oil mist separators Typ ON 1 and ON 2
Application areas:
- - Multi-spindle machines
- - Screw machines
- - gear milling machines
- - Circular- and Surface Grinding Machines
- - Cold forming machines
- - Drilling- and Thread cutting machines
- Etc.
Filter construction three-staged:
Aluminum stain filter and Special pocket filter for oil mist cutting efficiency higher than 98%. Filter stage with main filter F8 the cutting efficiency equals 99,5%.
The liquid resultat by the process of filtering is dripping in to a collector tub, which is emptied over a ball valve.
- - Service hour counter
- - Spinning direction display
- - Full engine protection an ON / OFF button
Technical specifications
Versions: | ON 1 | ON 2 |
---|---|---|
Ventilation | 1800 m3/h | 2200 m3/h |
Engine | 1,1KW | 1,5KW |
Connection | 1 x NW 160 | 2 x NW 160 |
Dimensions | 665 x 681 x 1872 mm | 665 x 681 x 1872 |
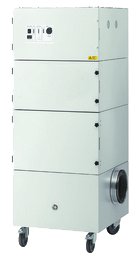
Oil Mist Separators Typ Losma
Serie Darwin 600, 1200, 2000, 3000
The Darwin Series with an extraction output of 600 to 3000 m3/h is very versatile. Because the outgoing particle acceleration of the Turbine (T) or the single centrifuge, respectively the double centrifuge (D), the oil mist will be absorbed. Through the centrifugal effect the absorbed fog is condensing directly and will be brought back to a fluid state. The created liquide will be taken away with a tub of drainage and is able to be resupplied to the machine.
The extraordinary filtration degree which the DARWIN Series guarantees can be even improved by using pre- and after filters. All air filters are combinable with these high efficient filter units, like that we are able to offer a variety of solutions.
Because of that proven modular system, quick adaptions are possible dependent of degree of pollution. The pre- and after filters, as well as additional systems are able to be added or removed at every time.
Application areas:
- - Multi-spindle machines
- - Screw machines
- - gear milling machines
- - Circular- and Surface Grinding Machines
- - Cold forming machines
- - Drilling- and Thread cutting machines
- Etc.
Inappropriate Application areas:
- - Absorption of other materials, which are not composed of pure or emulsified oil
- - Absorption of corrosive Steams
- - Absorption of explosiv materials in explosiv surroundings
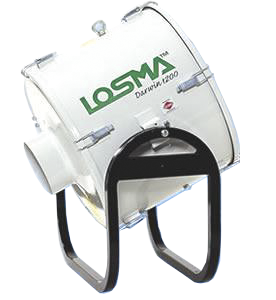
Versions:
Turbine (T): Filtration of emulsified oil mist and steam with many dirt particles
2 static stages
Single centrifuge (M): Filtration of pure and emulsified oil mist with a few dirt particles
1 dynamic stage
2 statische stages
Double centrifuge (D): Filtration of pure and emulsified oil mist with a few dirt particles
2 dynamic stages
2 statische stages
All versions are also available with stainless steel - especially used for oil- and micro mist with highly concentrated aqueous vapor like for example with washing machines or for the absorption of acidly or saline mists, smoke and steams.
Oil Mist Separators FOX IFS
Serie WS 250, 500, 1000, 1500, 2000
With a performance between 250 and 2000 m3/h, has the WS-Series, although it is coming with 3 filter stages, relativ small dimensions. If wanted, its possible to add one additional filter stage, to eradicate steams or smoke through a HEPA filter (with a performance of 99,95% MPPS according to EN 1822) or to eradicate gas and odors through highly absorbing performance with a activated carbon filter.
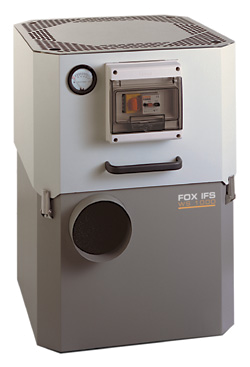
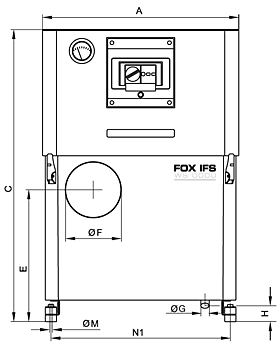
Application areas:
- - Multi-spindle machines
- - Screw machines
- - gear milling machines
- - Circular- and Surface Grinding Machines
- - Cold forming machines
- - Drilling- and Thread cutting machines
- Etc.
Garantierte Filterung:
- Phase: The pre filtering: with a progressively filtration through 3 partition walls, which guarantees a overall performance of 92% (effectiv G4 according EN 779) and also a excellent shelf life for solid and fluid pollutions.
- Phase: The centrifuge phase: A special rotor causes the filtration through centrifuging and continiously releasing the condensed oil- and emulsified particles.
- Phase 3: The final phase: With a high filter surface made of fiberglass does it has a performance of 99% (measured according to ANFOR NFX 4400). The degree of congestion is displayed with a manometer (included). According to this the moment to change the cartridge is clearly visible.
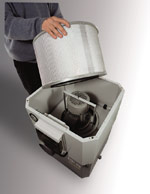